Heartburst
Location: Black Rock City, Nevada | Burning Man 2023 - Animalia Size: 30' x 30' x 15' Status: Completed Program: Temporary Spectacular
chevron_leftA Burning-Man Art Spectacular
The Heartburst spectacular was conceived by Benjamin Anderson, Christian Robert, and Shawn Gehle, the co-founders of OFFICEUNTITLED (OU), to express their deep appreciation for the art, community, and environment at the annual Burning Man gathering in Black Rock City, Nevada. This spectacular was brought to life by a remarkable team of designers, technical advisors, and volunteers. It is intended as a gift to the Burning Man community and encouraged attendees to engage with the spectacular and landscape, fostering a deeper connection with themselves and their surroundings.
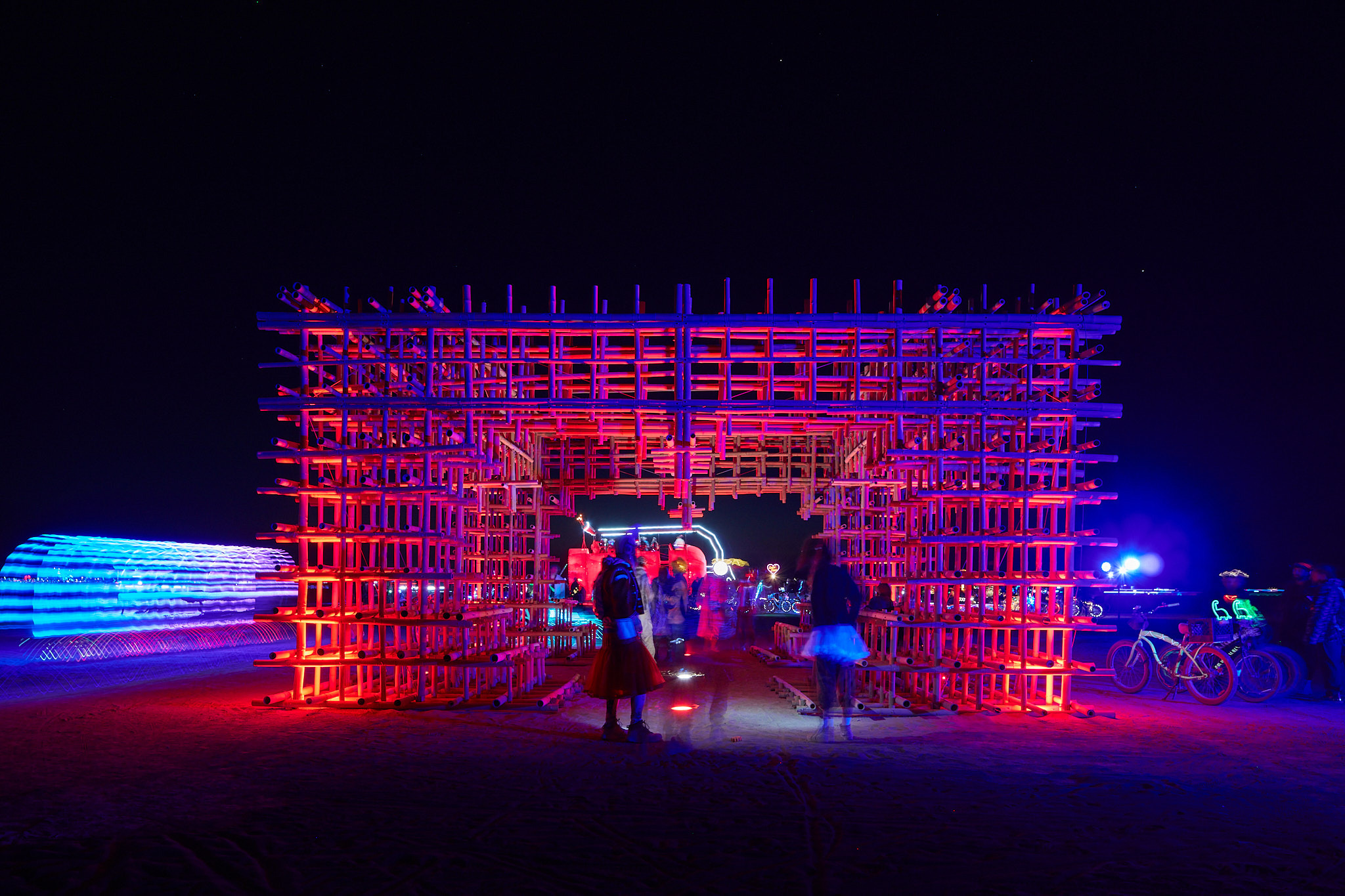
Make No Small Plans
A dry lakebed in the Black Rock Desert, commonly known as the Playa, is the home of Burning Man. Incredibly hostile yet beautiful, the landscape is dominated by the striking horizontality of the surrounding horizon and the vastness of the environment. Heartburst sought to create an anchoring moment within this greater vastness and introduce a human-scaled space that prompted gathering and reframed the landscape.
Celebrating the Potential of a Rapidly Renewing Material
The Spectacular encourages visitors to slow down, be present in their surroundings, and achieve a state of mindfulness, as Heartburst was designed to evoke physical, psychological, and communal coherence and healing. In addition to its sustainable nature, bamboo enhances the grounding experience of Heartburst, furthering human understanding of materiality in the built environment. Celebrating the simplicity of a natural material offers a calming and centering effect, promoting a deeper connection to the natural world and a greater sense of stability. Its four heart-shaped entranceways and shared internal intersections embody the power of diversity and promote coming together.
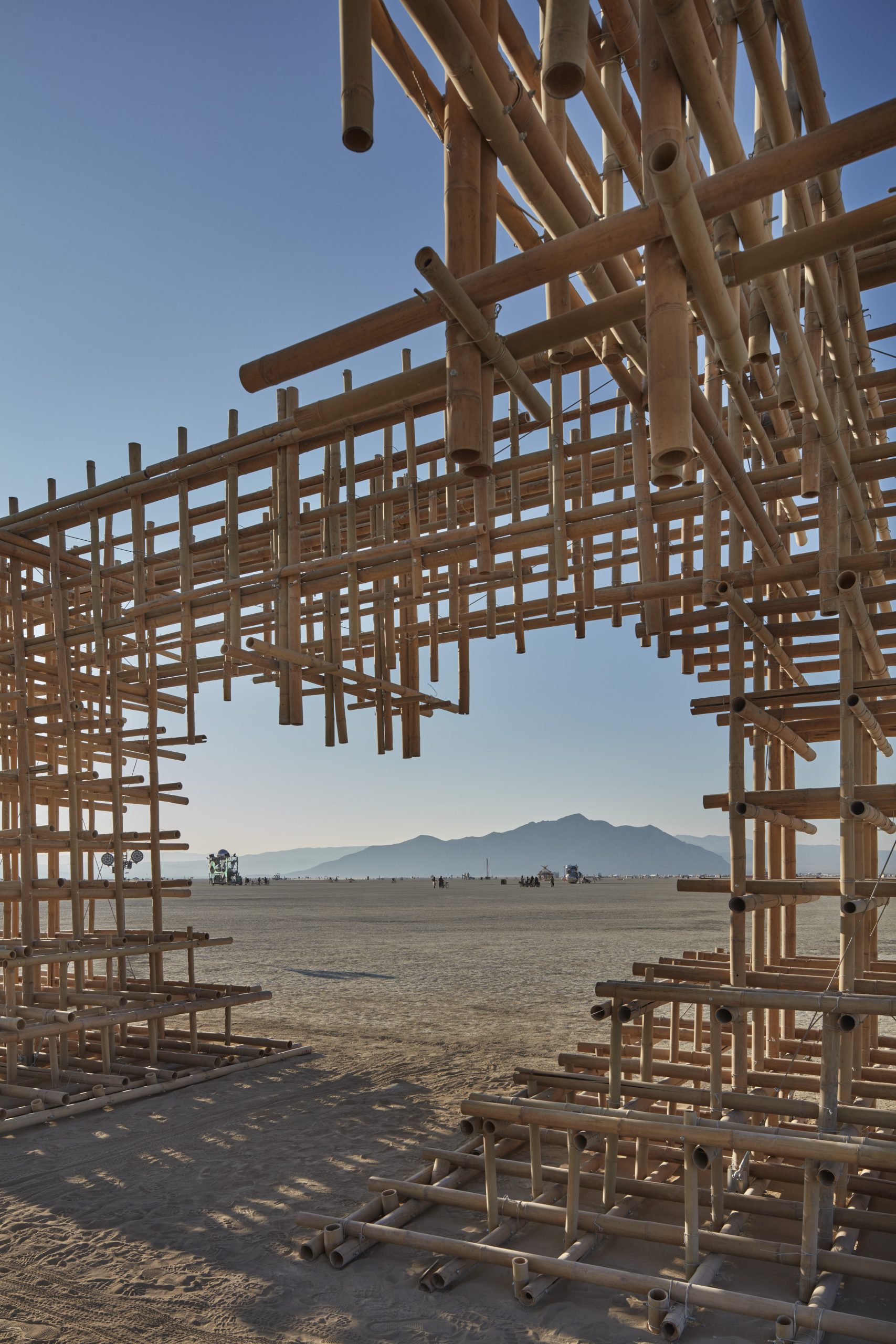
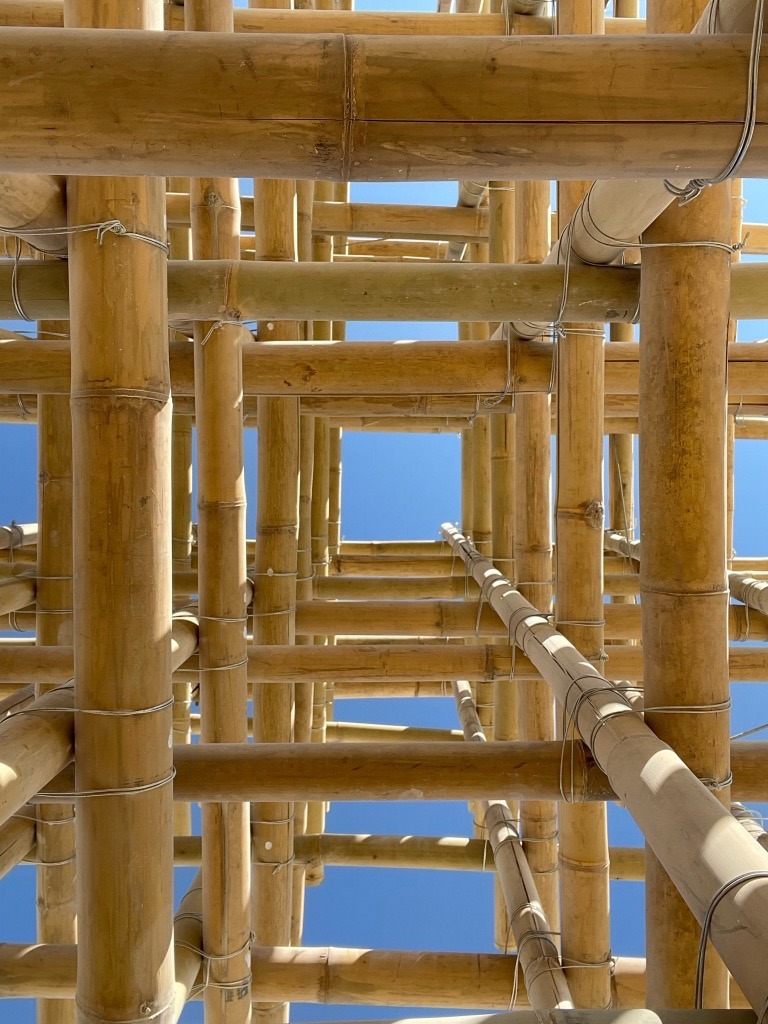
Materially Unexpected
An interest in furthering Burning Man’s sustainability goals is reflected in OU’s choice to use bamboo, one of the most eco-friendly and fastest-growing materials. By using bamboo in the construction of the installation, Heartburst advances OU’s commitment to environmental responsibility and demonstrates the possibility of creating stunning spatial experiences while considering the process and a project’s impact on the planet. OU worked with SEAD Build, a Malaysian bamboo company run by Lucas Loo, to ensure that Heartburst was created with a material that was environmentally friendly, sustainable, ecologically positive, and structurally durable. The bamboo used is not only more sustainable than other forms of timber but is “carbon negative” when considering the raw material, transportation, and production of the piece.
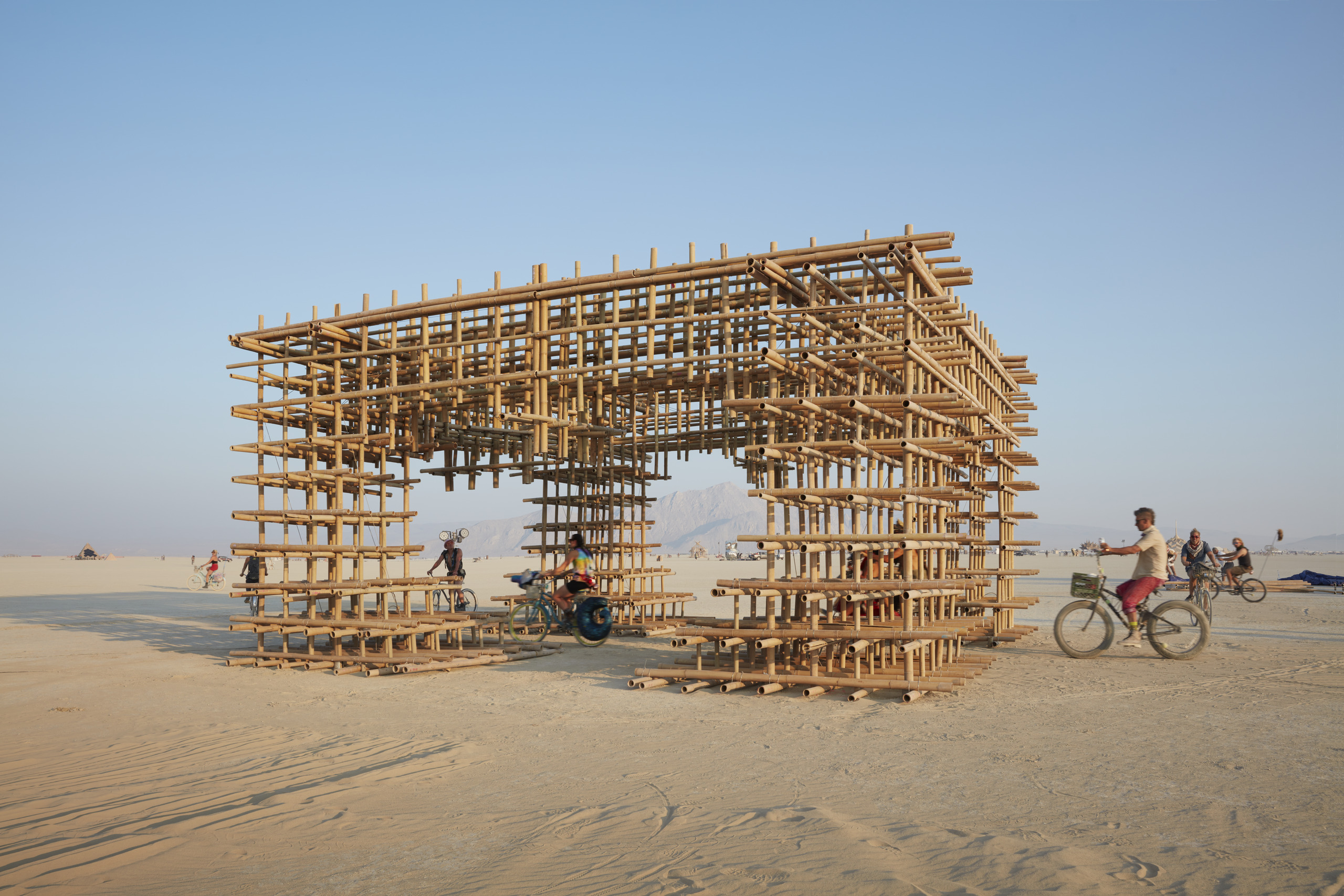
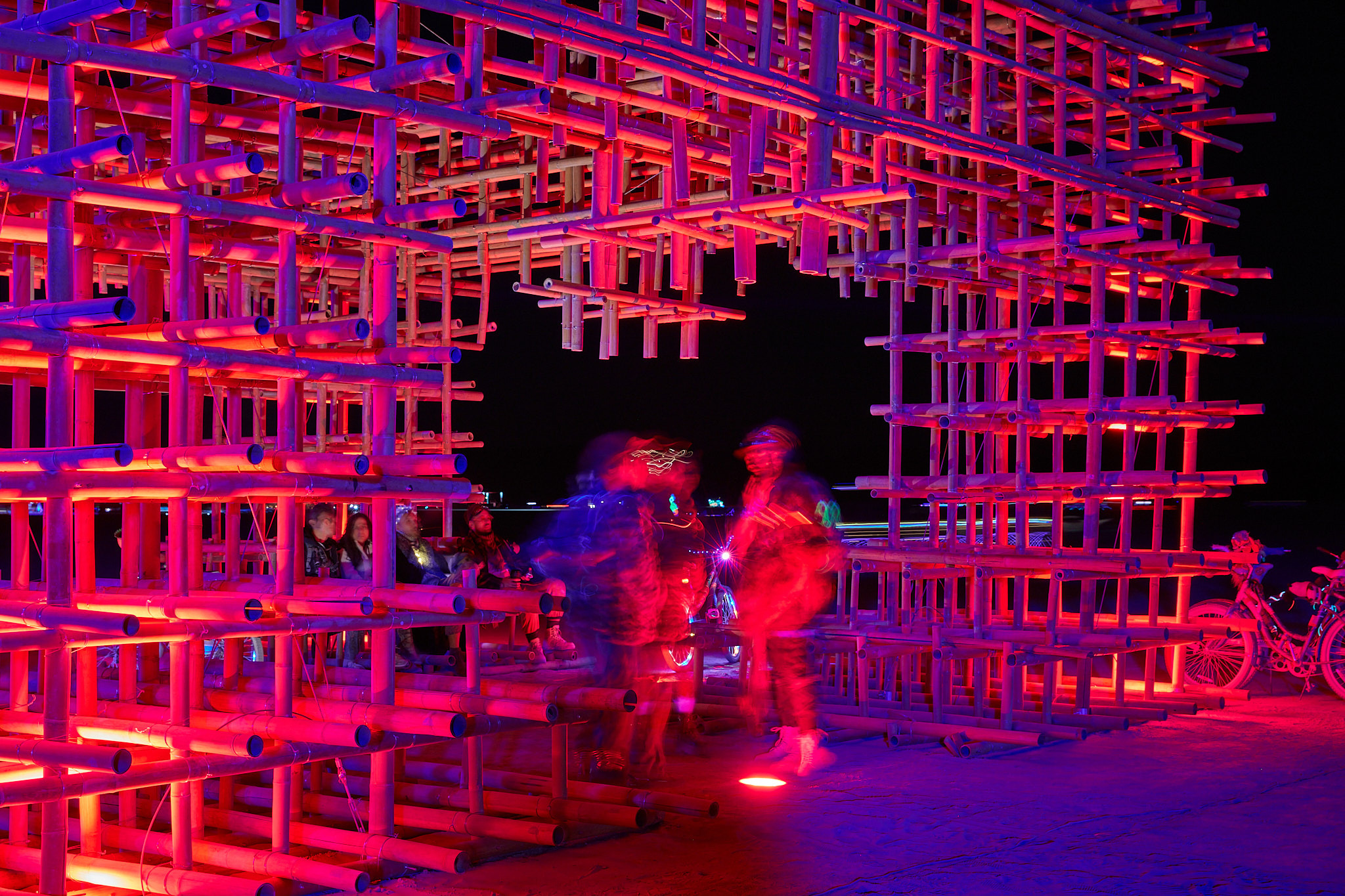
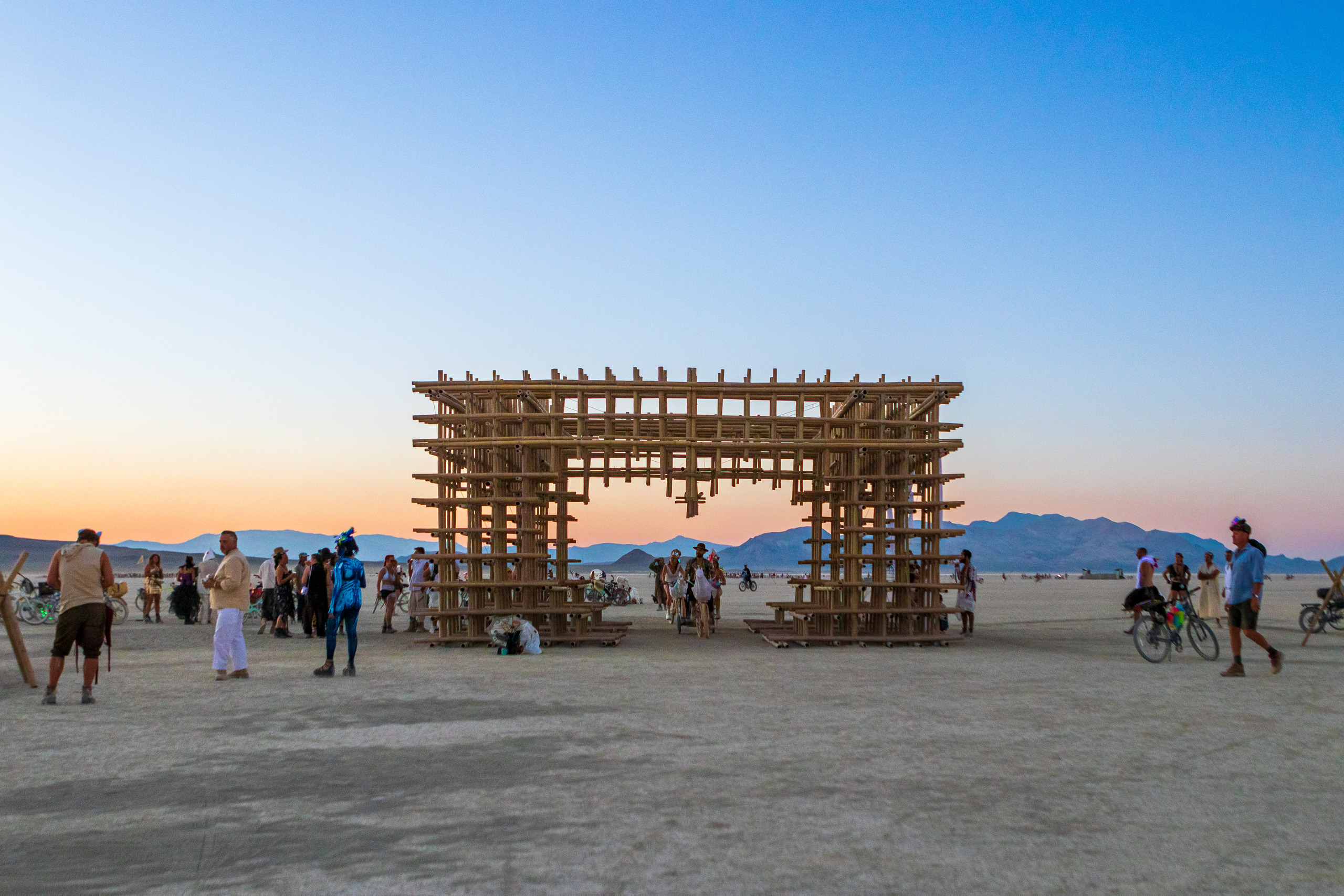
Conceived for Rapid Assembly and Disassembly
While Heartburst did require a large amount of hand assembly, it was rationalized for quick assembly during Burning Man’s build week and rapid disassembly following the close of the event. The structure’s system utilized traditional metal wire lashings and standard rebar wire tying tools to connect members, along with sixteen helical earth anchors to minimize the structure’s footprint on the playa’s sensitive ground plane. Several structural connections required bolted connections and were internally stabilized by diagonal steel cables with turnbuckles in anticipation of accidental climbing and wind gusts reaching up to 75 mph.
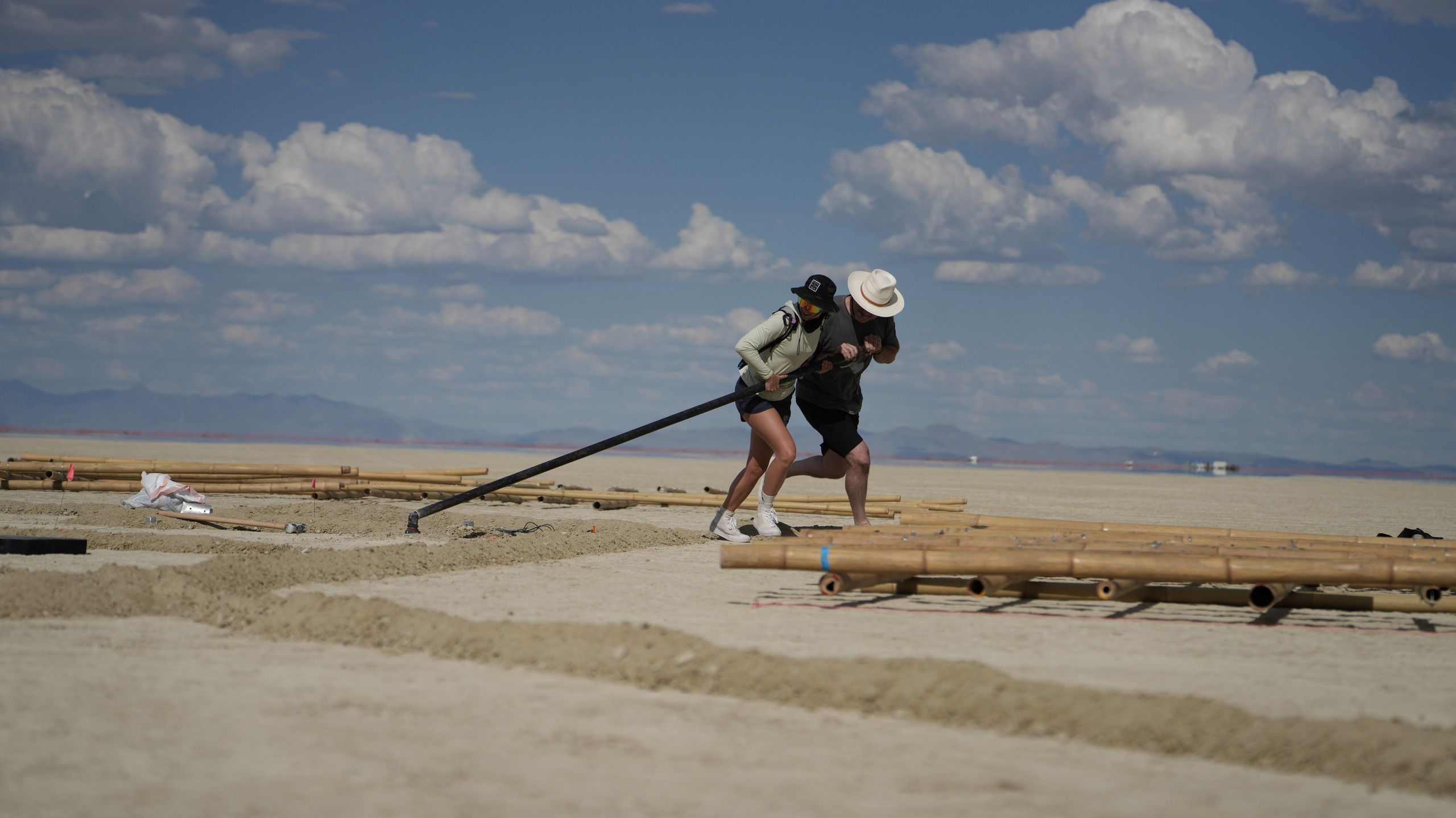
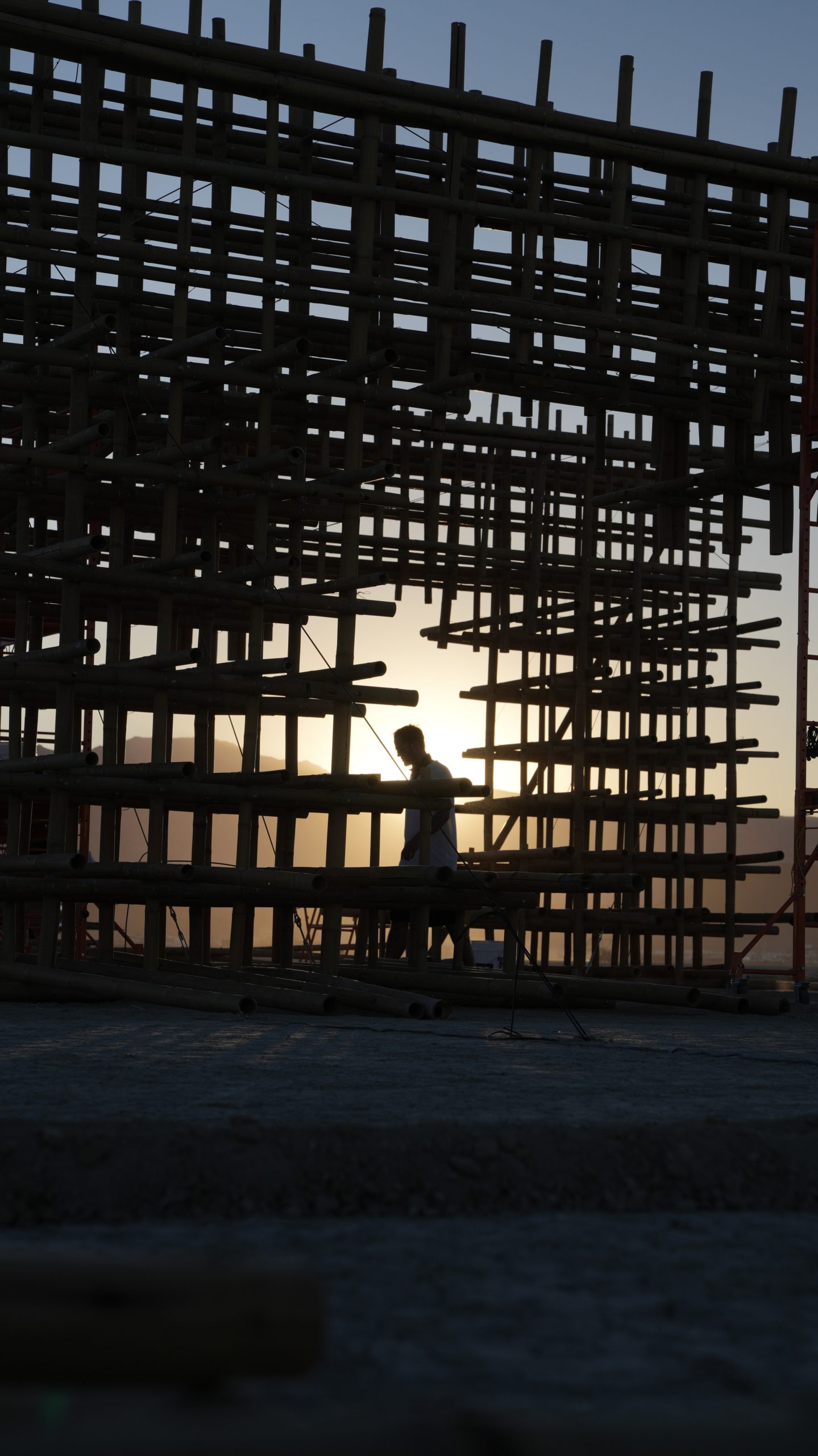
Each gridline or “slice” was composed of up to six prefabricated panel sections, specifically designed and fabricated around the limitations of a standard 26-foot box truck. The prefabricated panels were assembled at OU’s Culver City office before being transported to Black Rock City for final assembly and erection on the playa.
The bamboo was categorized and tracked using three consecutive systems:
1. The first system was employed by the Malaysian team, designating the precut length of bamboo pieces being shipped.
A simple color marking at the end of each member was added, accompanied by a note clarifying whether each member
was structural or non-structural.
2. The second designation labeled large, prefabricated panels, indicating where each panel was to be placed within
the overall sequence.
3. The third and final designation sorted the loose poles according to their installation height and location.
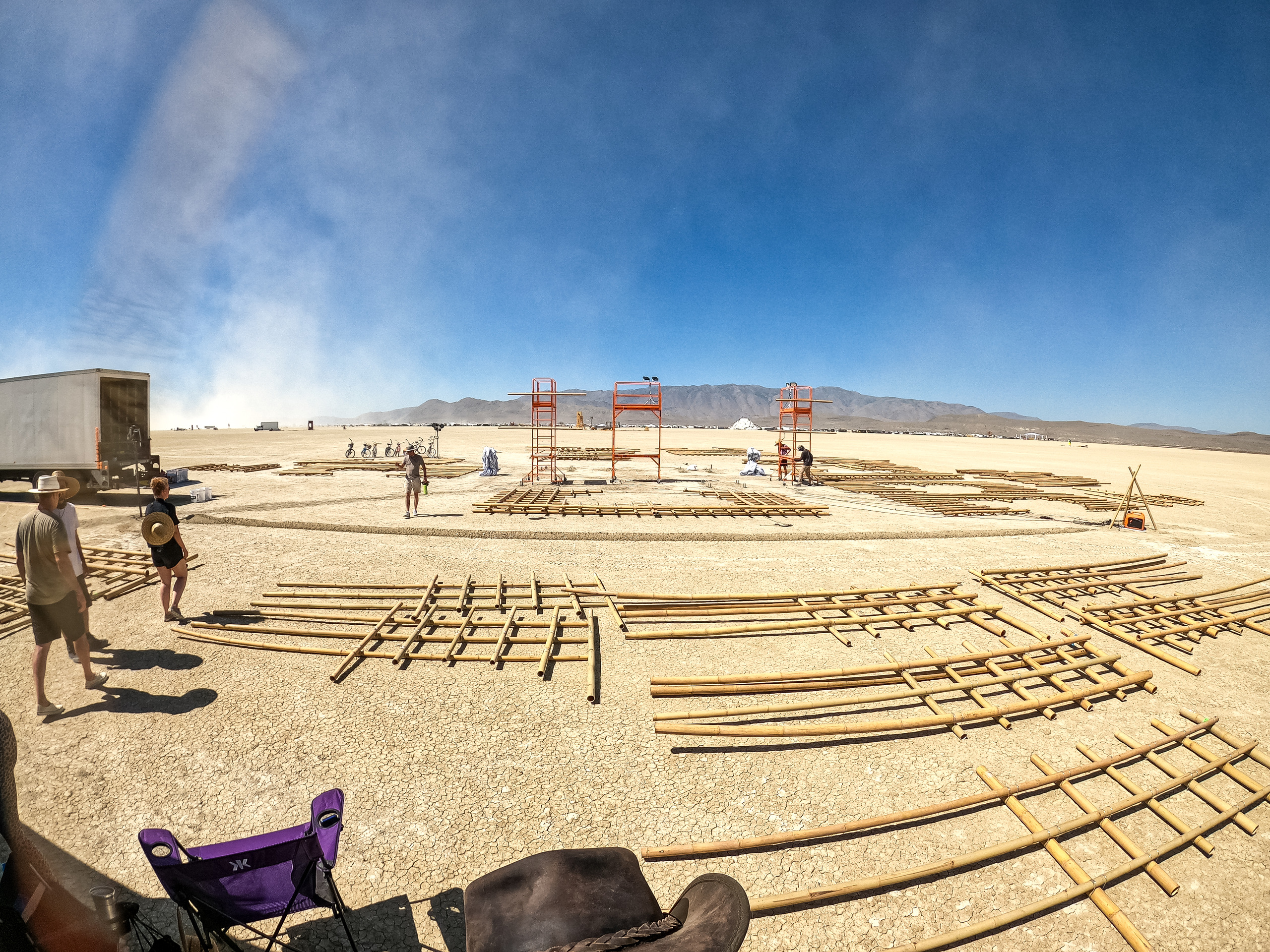
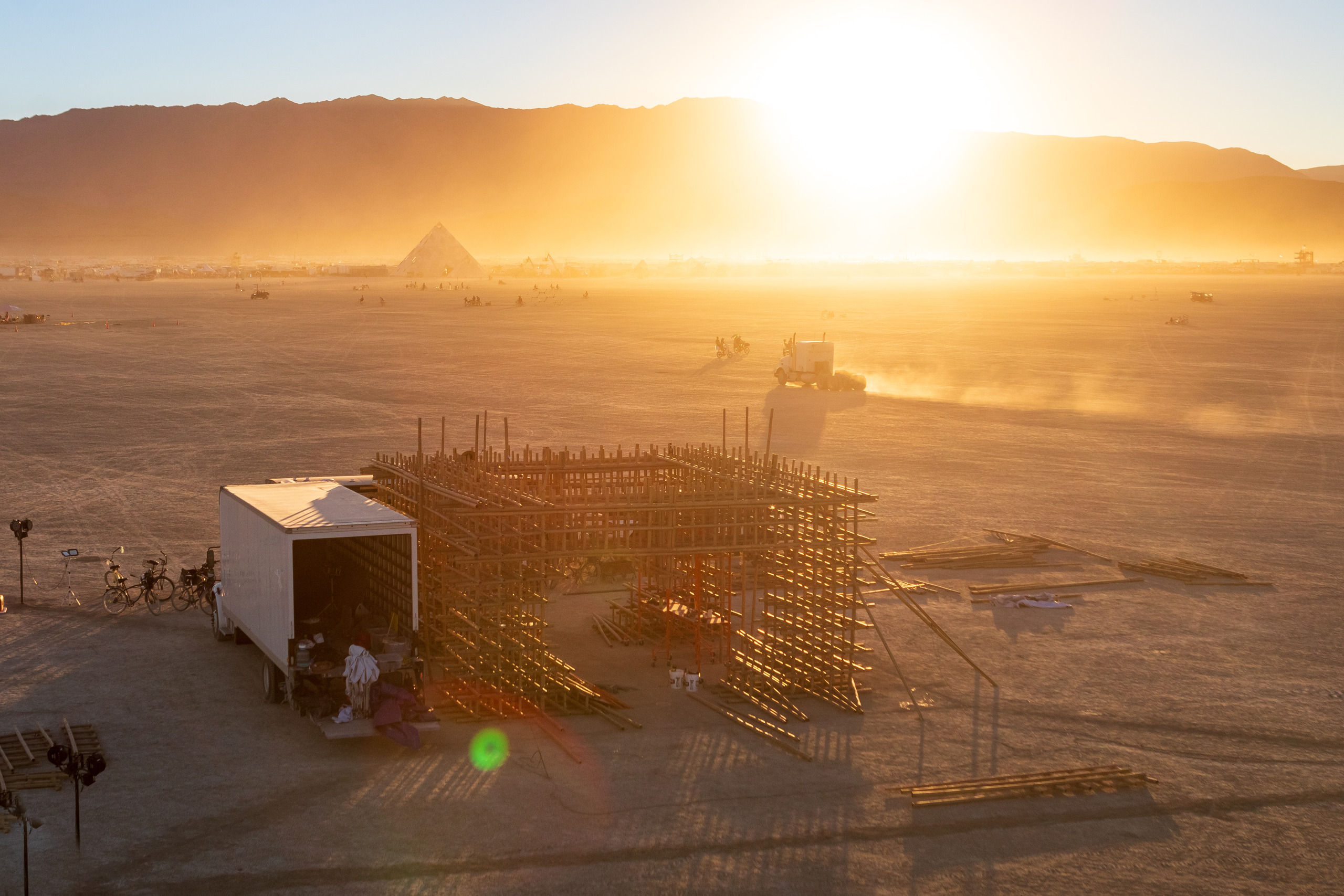